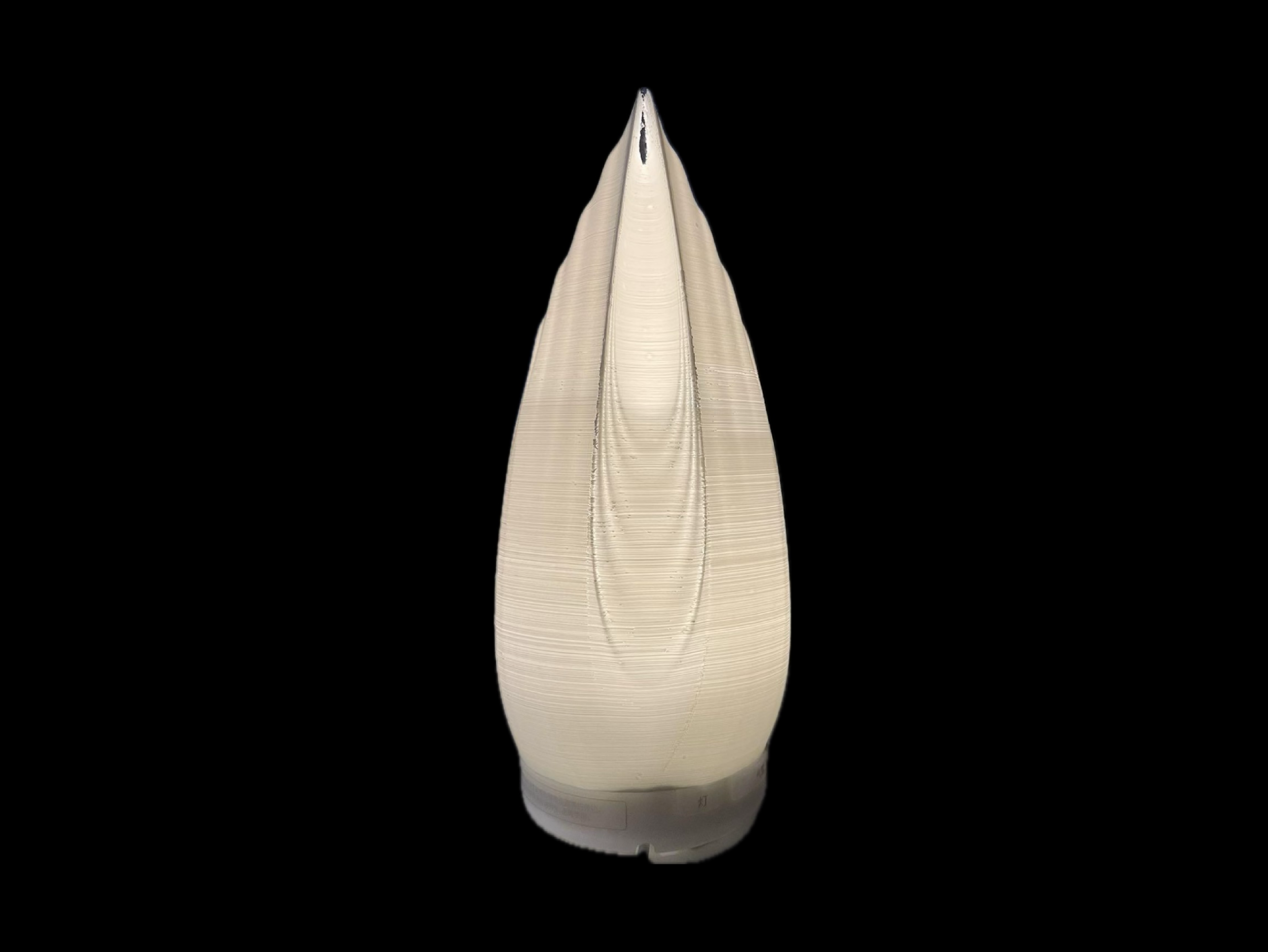
Free Form Lamp
Contributors: Qiushi Chen (Design in Rhino7, Fabrication in Cura and Anycubic PLA printer)
Instructor: Alex Ion
Duration: 1 week
Link to live video documentation
Thingiverse Link
Hello, World! To be Updated 3D Design Pan-Around Preview
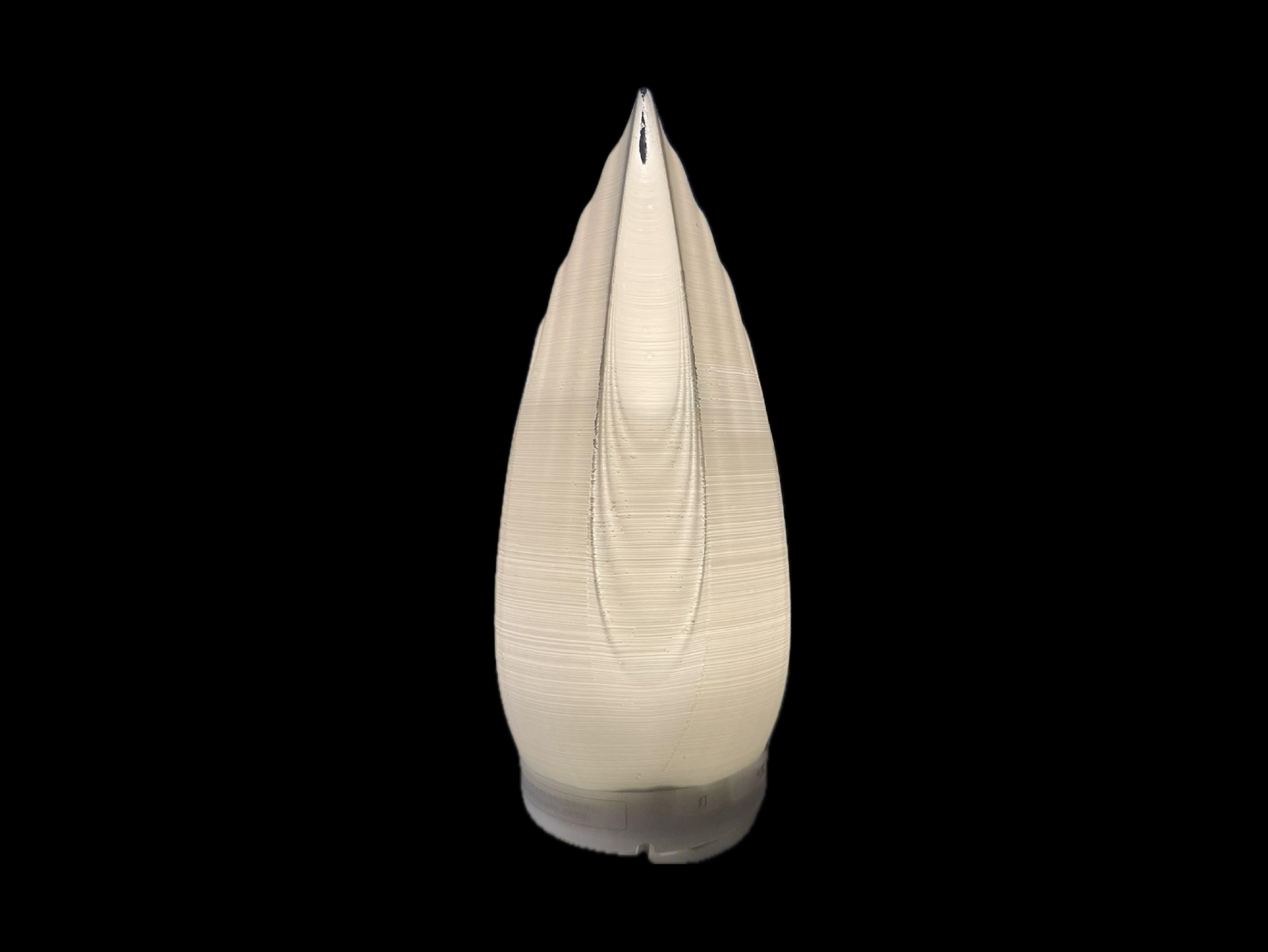
Project Brief
Since I moved to the US for college and live in a studio apartment, essence diffuser has become one of my favorite artifacts that gives fluctuations, changes of mood to the static interior spaces by diffusing different types of essence oil and emitting dimming lights at night. However, I think the design of the MUJI model I currently own is too simplistic and monotone. Thus I want to make a statement with different formal language that better expresses the function it embodies - introducing changes to the interior space. The Sub-D modeling feature is one of the major updates in Rhino 7 that I had little experience with before. It marries the mesh and NURBS modeling logic and enables direct rapid modifications on any Sub-D freeform geometries. Thus I think it's a rewarding chance to learn and try out Sub-D modeling in the Final Project development.
Comments on Design Language across Different Scales
As an architecture student, I have always been interested in the various statements architects made on smaller scales (eg. lamps or chairs) that later evolved into building scales. Some examples I personally love: ) The biggest thing I learned is to develop personal design language afforded by technology and zeitgeist. Sometimes architectural ideas can live in a scale of lamp.
Design and fabrication Process
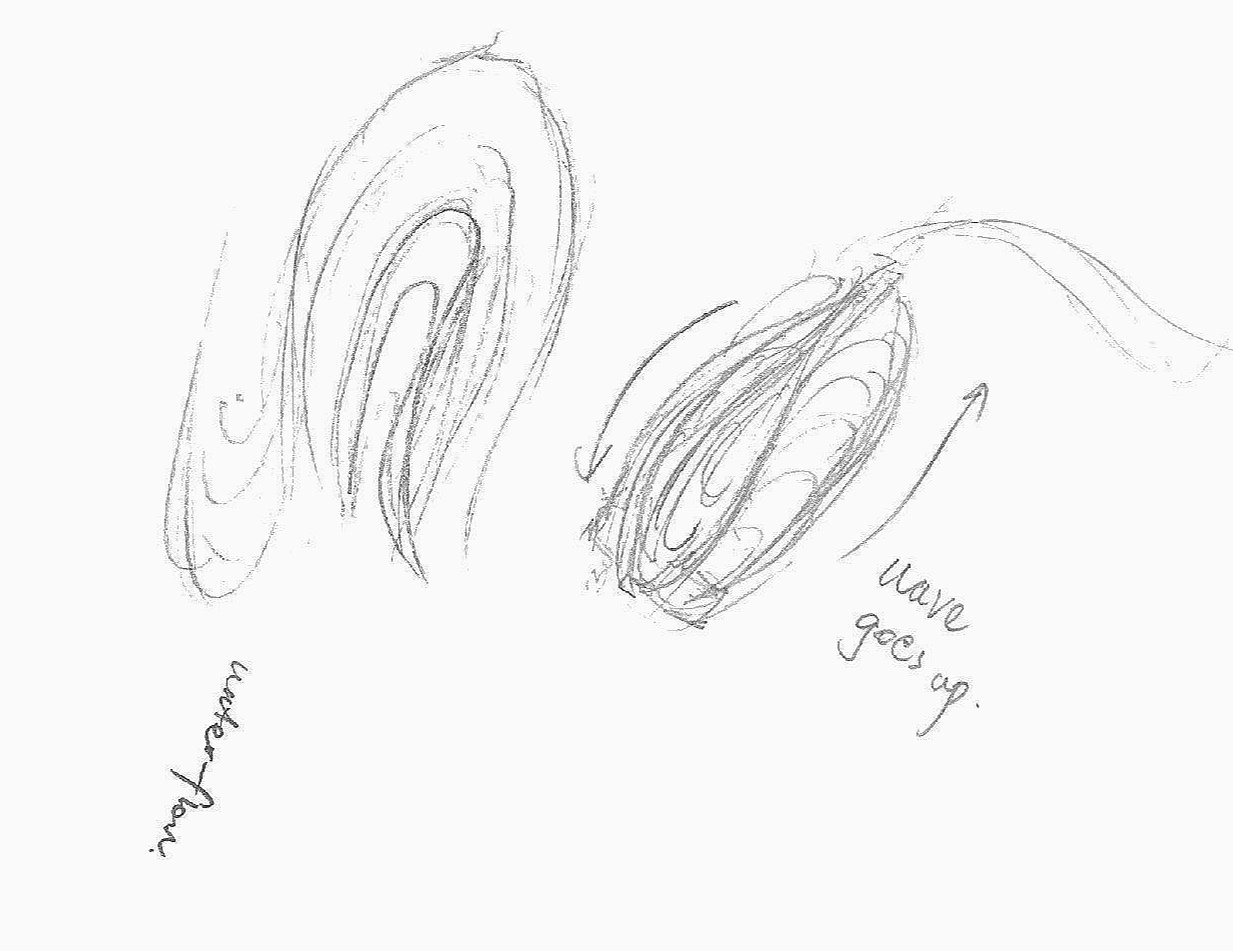
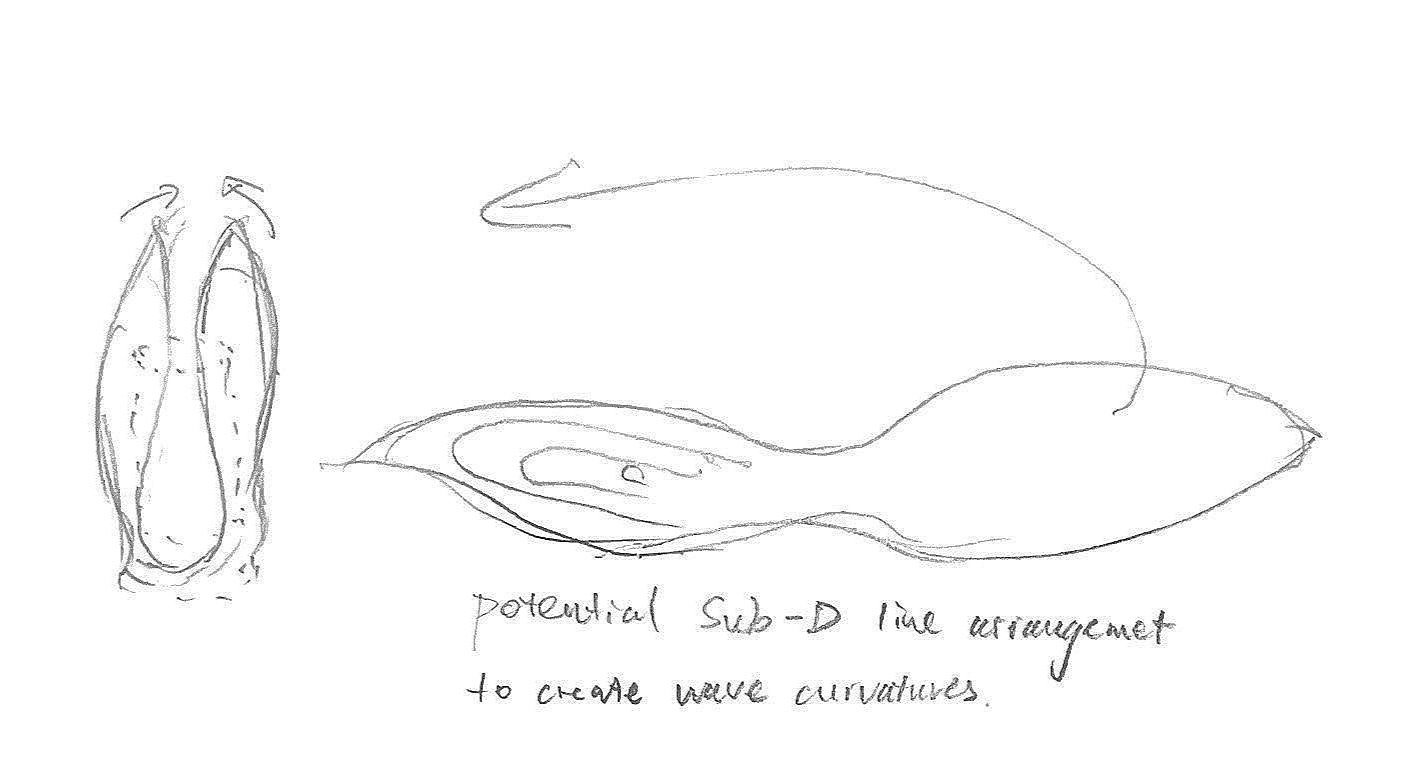
1. I started off by sketching wavy ripples of drips to generate the form strategy and think about potential way of subdivisions in surfaces:
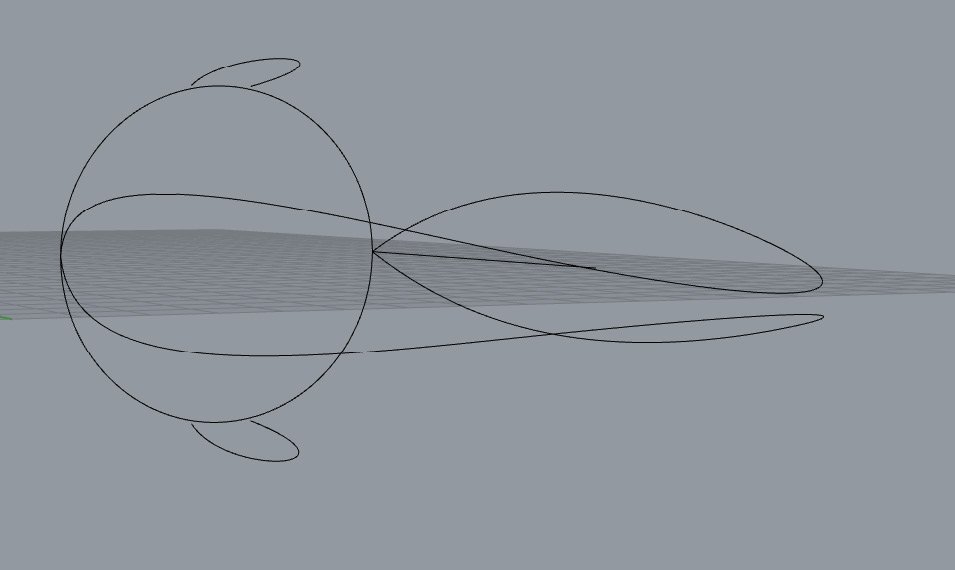
2. Drive Curves in Perspective
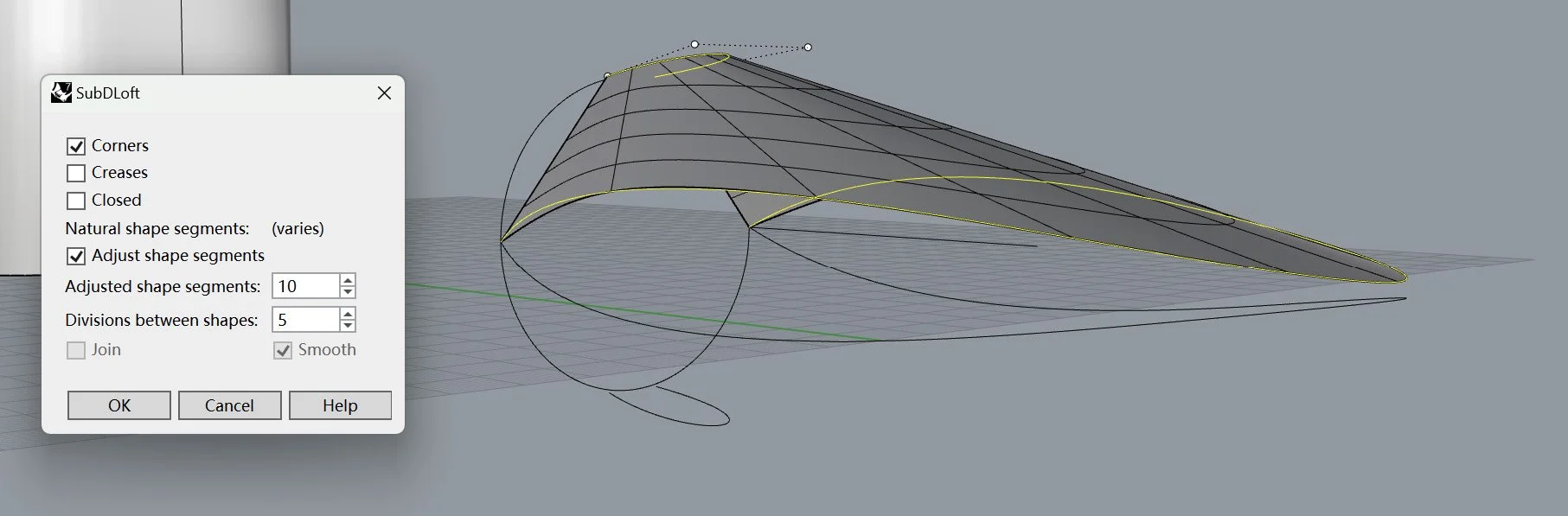
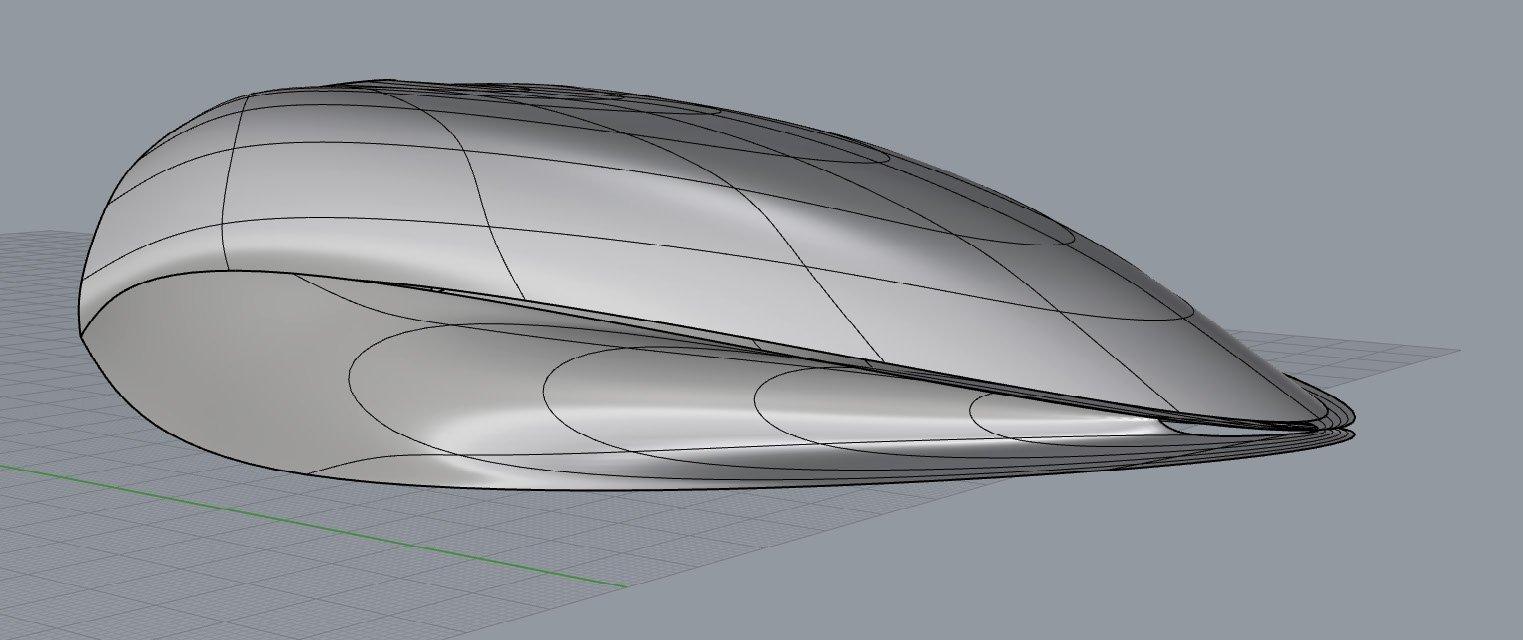
3. Use the Sub-DLoft command on nurbs curves to generate the surfaces. I decided the partitions parallel to the drive curve to be 5, and vertical ones to be 10, since I need accurate shape and easy adjustments to fit the cylinder base. The seam condition between two surfaces was not closed at the first attempt. I managed to use the sub-d mesh edge of the middle surface to loft an upper nurbs curve to create the upper mesh surface, thanks to the Sub-D adaptability. This creates seamless connections between the two surfaces.
4. Use gunball to rapidly manipulate the the partition lines to change the overall geometry to fit the base and test fit the cylinder base to make sure of no collisions happen between the base and new surface:
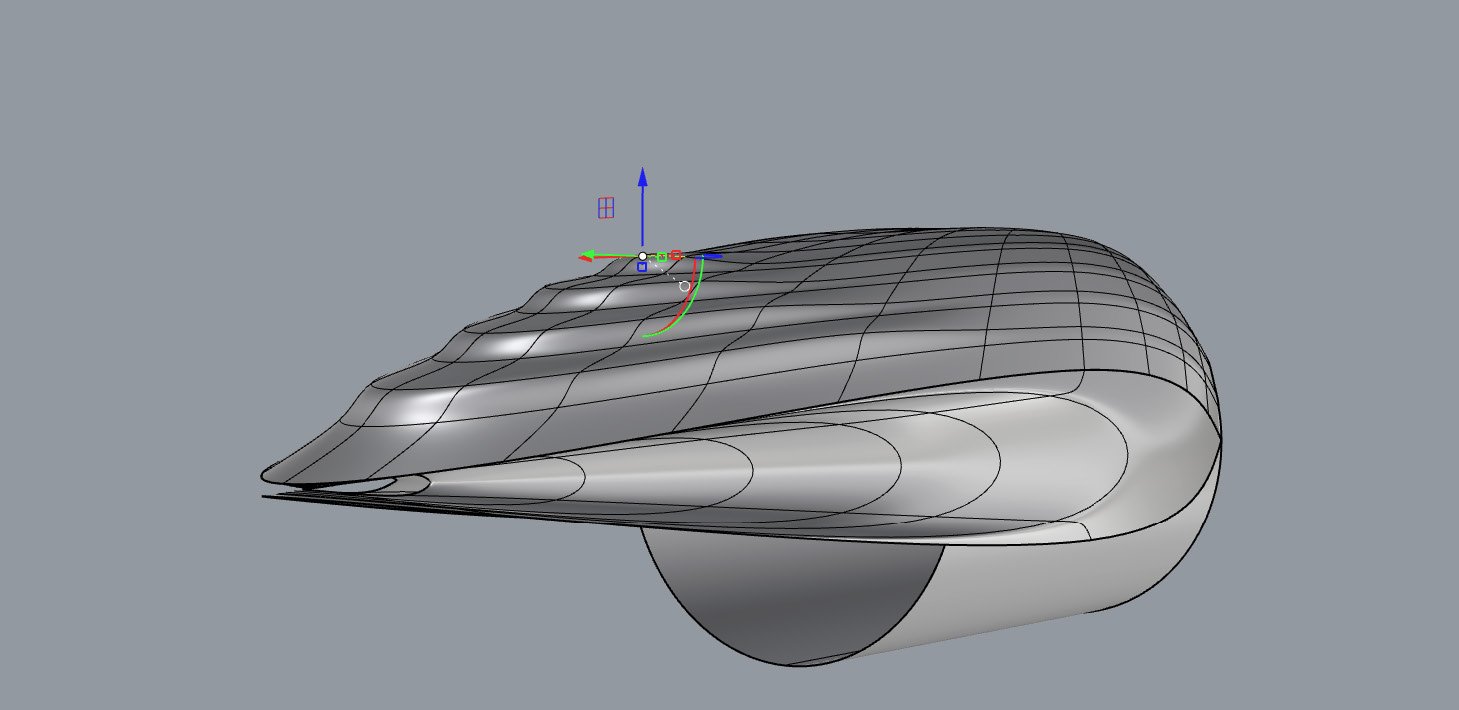
